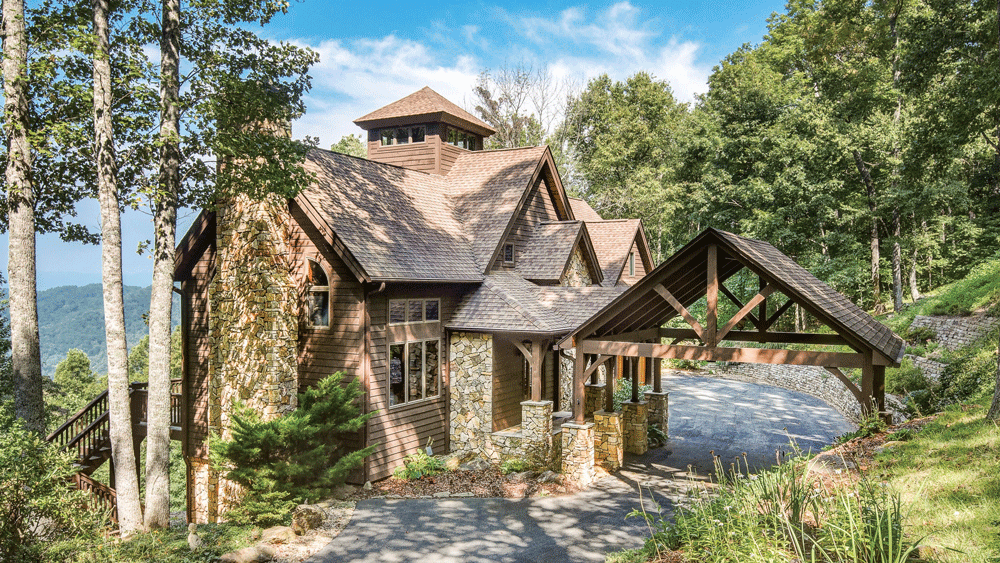
Today we ask a lot from our homes. They must not only shelter us from the elements, they must also be secure, energy efficient and good looking. When we build houses we also look for a solid investment that will last for decades.
Timber frame builders have responded to modern concerns by investing considerable effort in professional engineering and design to ensure that their frames will meet today’s needs and standards and will withstand the test of time.
In simplest terms, every solidly built timber frame contains hundreds of timbers working together to form a resilient self-supporting structure. Every joint is designed to transfer loads and stresses from one member to another. Each timber is positioned and sized to transfer a share of the building load through the frame to the principal posts and on to the home’s foundation.
Although the actual engineering of your frame will be left to the experts, you may find it useful to have a better understanding of the basics of a timber frame — from the wood species used to the joints carved into the wood. The photographs in this article will show you some of the basics and your timber frame designer should welcome the opportunity to elaborate on the specifics in your frame.
Which Wood for Your Timber Frame?
A wide variety of wood species can be used to build modern timber frames, but it’s important that the wood selected is appropriate to your frame’s design. Wood species vary in strength and timbers must be sized according to their structural design values.
Just about any wood can be used to build a timber frame as long as the strength characteristics of the species are taken into consideration. If your frame is fashioned from a strong wood such as Douglas fir or oak, your frame would have smaller members and a lighter look. Weaker woods would require larger members.
Typically, timber framers work mostly with one species of wood or with a carefully chosen repertoire of woods. They will be able to design your frame with a particular wood’s characteristics in mind. In fact, many timber frame home buyers choose a timber framer largely because they like the look of a certain timber framer’s wood species and how that species influences the design of the frames.
Because seasoning the large pieces of wood needed for a timber frame would take several years under cover, most timber framers use green, or unseasoned, timber to build their frames. Green timber is easier to work with tools because some woods become very hard when dry.
Green timber will shrink as it dries, and timber frame builders must calculate shrinkage into a frame’s design. While good joinery design is the best precaution against excessive shrinkage, shrinking timbers are sometimes held in place by the use of drawboring. In drawboring, peg holes are drilled slightly offset, so that the peg must take on a curve to follow the holes. In doing so, the peg acts as a spring, pulling the joint tight as it shrinks.
As the green timbers in your home dry and shrink, they will develop surface cracks or splits. These cracks are called checks. Checks do not affect the timber’s performance but merely indicate that the timber is seasoning. Most timber framers use proven strategies to minimize checking, such as applying paraffin to the end grain of timbers to slow the drying process. Other common strategies include working with a certain cut of wood or species of wood, especially in prominent locations in the frame. You can help minimize the checking in your frame by not overheating your home during the first few winters you live in it and by making sure the air in your home has adequate humidity.
Using Recycled Materials
More and more, people are salvaging old timbers from old barns, homes and industrial buildings. Salvaged timbers that have been standing for several decades or centuries are already dry and will most likely not shrink any further. While it’s difficult to predict where a green timber will check, any checking that has occurred in old timbers is visible and can be hidden in a new home. Recycled timbers are often re-sawn to remove any twist or warp that occurred as they dried.
The work involved in salvaging recycled timbers makes them slightly more expensive than green timbers. After the old structure is dismantled, the timbers must be re-worked. First, nails are removed. Then the exterior weathered wood is skimmed and planed smooth. However, if the builder wishes to retain the original hand-hewn finish, the timbers are steam cleaned instead of planed. Drier wood is more difficult to work, which also adds to the cost.