Timber framing is backed by a rich history of strength, beauty and durability. Yet, for many years, the high level of craftsmanship at the heart of this centuries-old tradition fell out of favor as a quantity-over-quality mindset pervaded home building. Then, about 50 years ago, timber framing found itself back on the building scene in a big way. The timber frame revival coincided with the arrival of SIPs, structural insulated panels, and ICFs, insulated concrete forms — two peak performers when it comes to time and energy-cost savings.
SIPs
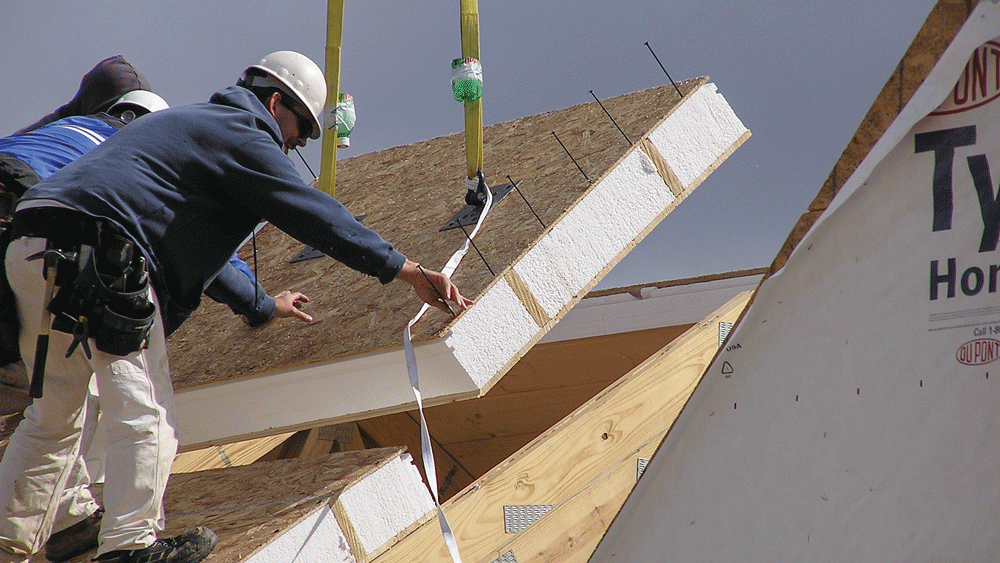
Photo: Eagle Panel SIPs
What are they?
“SIPs are made by laminating two pieces of performance-rated OSB2 around a solid core of expanded polystyrene foam insulation,” explains Stephen Munn, general manager of Insulspan, a leading SIPs manufacturer.
How are they used?
Large structural panels enclose the timber framed (walls and roof) structure. “SIPs are the highest quality construction material to quickly and efficiently wrap a frame,” says Stephen.
What are the benefits?
- Speed of construction + less waste + lower labor costs. Often, panels include pre-cut openings, which accelerates the construction process and reduces job-site waste. One company, Eagle Panel Systems, has taken SIPs construction savings to a new level by pre-finishing its roofing panels with eastern white pine tongue-and-groove. “With these INTEGROOVE® laminated SIPs, you have your framing, insulation, intermediate board and tongue-and-groove pine all going in at once, so we’ve taken care of four steps in one,” explains advertising manager, Vicki Disch. “You get a finished roof/ceiling that can be set in minutes, as opposed to weeks.”
- Energy efficiency. The impressive R-values of the panels, coupled with the installation method, produces an airtight building envelope. Stephen explains: “Because of the large panel sizes, fewer studs are needed, which reduces heat loss and air leakage. Then, each joint is sealed with a SIPs sealant that reduces air flow through that joint.” An additional benefit: The tightness of the thermal envelope means a smaller HVAC system is required to keep interiors comfortable. This translates into cost savings over the life of the home.
ICFs
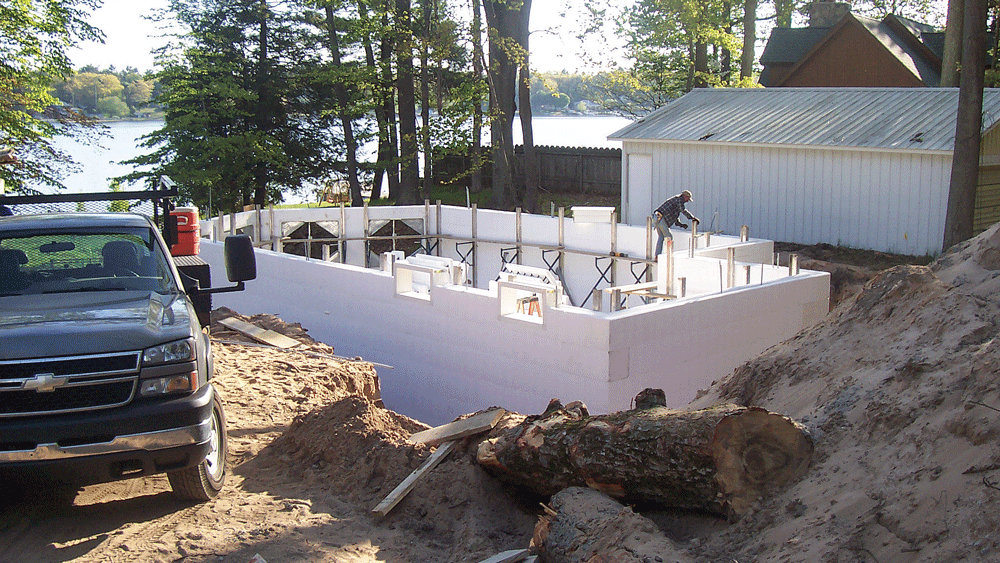
Photo: Logix
What are they?
ICFs are hollow blocks made from expanded polystyrene (EPS). Often compared to Legos, they feature an interlocking design and are reinforced with rebar and filled with concrete. Once filled, the forms stay in place.
How are they used?
In timber framing applications, ICFs are used in basements or crawl spaces to build foundation walls.
What are the benefits?
- Ease of construction + lower labor costs. Like SIPs, ICFs allow onsite construction to proceed quickly and smoothly. The foundation walls of even complex, custom footprints can be built easily with ICFs, and because the blocks are pre-insulated, there is one less step (and tradesperson) needed in the construction process.
- Energy efficiency. While the specific R-values of ICFs vary by brand, they consistently outperform concrete block construction, resulting in a more comfortable lower level. ICFs also have R-values high enough to avoid having to insulate floors. “That fact alone results in a substantial savings that offsets the additional upfront cost to using ICFs,” explains Buddy Hughes, territory manager of Logix Insulated Concrete Forms, a major ICF brand.
- Pest control. Some ICF brands go the extra mile by offering termite-resistant ICFs. “During the manufacturing process, we add a powder that kills tunneling insects,” explains Buddy. “From speed of installation to efficiency to termite resistance, all of these benefits combined make using ICFs for basements a no-brainer. There’s just no reason to build a basement out of anything else.”
See also: Q+A: Wiring a Home Built With SIPs