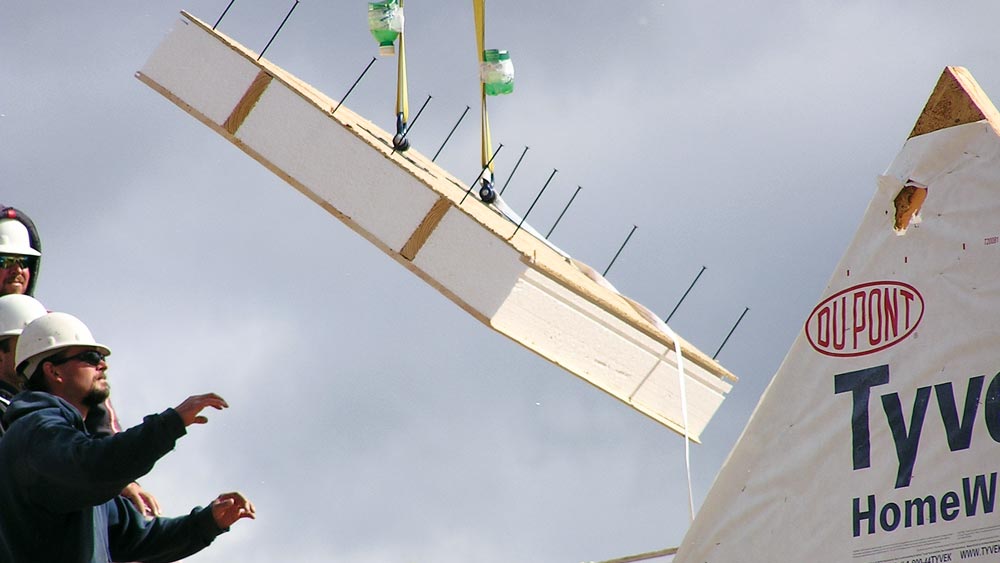
Photo: Eagle Panel Systems, Inc.
A timber frame home needs walls, and SIPs (structural insulated panels) are the most popular way to enclose it. Although individual manufacturers’ products may vary, fundamentally SIPs have a solid core of insulation sandwiched between two layers of oriented strand board (OSB). Other materials used in SIPs include plywood, wafer board, sheet metal and gypsum board. The white core is typically polystyrene, extruded polystyrene, Styrofoam or polyurethane — the same durable-yet-lightweight foams used in bicycle and motorcycle helmets — and can be enhanced with graphite for an even bigger boost to already impressive insulating properties.
How are SIPs applied to a house? “When I meet with new clients, I ask them to visualize a 12-foot-long wall; with conventional construction that wall has ten 2-by-6 studs, each acting as a small post. The insulation is then incorporated between each of the structural members, allowing for thermal bridging (gaps) at each stud and lowering the cumulative R-value of the wall,” explains Jeremy Bonin, principal partner and lead architect at Bonin Architects in New Hampshire. “In a timber home, on the other hand, large SIPs are applied to the exterior of the frame, almost eliminating thermal bridging and providing a more continuous airtight structure.”
The amount of energy you can save by choosing SIPs depends on the size of the home, but consider this: A 2-by-6 stud-framed wall using R-20 fiberglass batt insulation achieves an effective R-value around 16.8, while a 6.5-inch thick SIP wall can reach R-22 or higher. The thickness, material and type of insulation you choose for your roof plays a factor in how energy-efficient your home will be.
SIPs have a higher up-front cost than other types of insulating materials, but according to Stephen Munn, general manager of SIPs manufacturer Insulspan, the ROI is well worth it.
“When you factor in the speed of construction SIPs provide, buyers actually can save money during this stage of the project,” Stephen explains. “The real savings, however, is what owners will see over the life of the home. With SIPs, the house requires a smaller HVAC unit, thanks to the higher R-value of the walls and reduced air loss, so the equipment costs less. Then you can save even more money on energy usage over time due to fewer air exchanges. These are the long-term savings that make SIPs worthwhile.”
SIPs Tips
They’re flexible.
SIPs can arrive at the home site in bundles of large generic panels that builders cut to fit the home’s specific floor plan. Or panels can be cut exactly to the home’s design at the factory by the manufacturer and then numbered for easy installation, which results in less wasted materials and onsite resources.
They’re energy efficient.
SIPs cut heating and cooling costs by as much as 60 percent over products used for conventional construction. Even where wall thickness is the same, SIPs outperform stick framing on whole-wall energy performance by 40 to 60 percent.
They’re environmentally friendly.
Many SIPs components come from renewable or recycled resources. The oriented strand board (OSB) that encloses the foam core is made from fast-growing trees and wood chips once considered waste by the lumber industry.
They’re soundproof.
SIPs block sound like few other materials — a big perk, especially in bedrooms, dens, home offices and media rooms.
How Much You Save
According to a study conducted by the Structural Insulated Panel Association, the average homeowner who chooses SIPs will recoup his/her investment in 5.7 years in the U.S. and 2.7 years in Canada. Learn more about SIPs at sips.org.