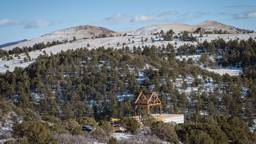
Photo: Mark Sorenson / This aerial shot emphasizes the solitude of the site (and gives you a sense of the challenges the Timbercraft crew overcame with the rugged terrain). When the home is done, Peg and Tony will enjoy peace and quiet along with their sweeping views.
It’s the quintessential image that comes to mind when you imagine building a timber frame home: A web of posts, beams and trusses rising above the snow and rock, built to withstand generations of seasons. It’s a work of art, and the day those beautiful timbers go up and are enclosed with structurally insulated panels — frame-raising day — is a lot of fun, too.
Timbers should arrive at a job site once the subfloor is set atop the foundation. A crane will unload the bundles of wood and stack them near the home’s future front door for easy access.
Our homeowners, Peg McVay and Tony Stramm, are building a hybrid timber frame home from Timbercraft, a choice that means once the frame is in place, the crew also erects the SIP walls, which will assist in supporting the timber ridges and plates. Normally, there’s one or two people “in the air.” That may be with scaffolding or a man-basket, but what they’re doing is catching the timbers from the crane and plugging the beams into their pockets. President and CEO of Timbercraft, Bob Sternquist, describes this as “a grown man’s Lego system.”
“You know what’s nice about building a timber frame?” asks Bob, “It’s almost like ‘Extreme Makeover: Home Edition,’ because you get this visual reward every evening when you’re done. On Day 1, your ultimate goal is to get the truck unloaded and maybe get two trusses erected. By the end of Day 2, you typically have the whole great room up. The entire structure usually takes three days, but it can vary between manufacturers and the size of the home. At Timbercraft we pre-fit everything front-to-back and left-to-right. There’s really no field modification at all.”
According to Bob, that speed of construction is one of the main reasons buyers and builders are migrating towards the aforementioned SIPs. “Usually when you’re using conventional framing, you’re framing a wall, you’re putting sheeting on it and you’re standing that wall up. It’s a slower process,” he explains. “With SIPs, the largest pieces of oriented strand board (OSB) are 8-by-24-foot sheets so we’re building potentially 8-by-24 sections of walls and roofing that already have all the insulation built in. And, if you utilize our urethane panels, we’re actually putting the electrical boxes and conduits in the panels ahead of time.”
These advantages, coupled with the timeless beauty of exposed timber framing are a few of the many reasons why more home buyers are discovering and choosing timber frame homes.
Stay Tuned!
Join us as we navigate the design process with the homeowners and Timbercraft. You can find all the latest installments of the Dirt to Done series in the print magazine and here on timberhomeliving.com. Plus! Stay tuned for new webinars that dive into the process of creating this home.