Outside of Cañon City, Colorado, on the top of a hill and under the ever-present gaze of Pike’s Peak, Peg McVay and Tony Stramm are in the home stretch — they’re finishing the interior of their hybrid timber home, where victory would mean obtaining their certificate of occupancy by month’s end.
But on the October day we spoke with Peg, she and Tony were just putting the final touches on the home’s plumbing. The electrical rough-ins had been installed the week prior. The kitchen is painted and most of the cabinetry is in; however, they’re missing one base cabinet so they can’t measure for their granite countertops quite yet. These kinds of issue-related delays are par for course in any custom build.
Tony understands this better than anyone. As a contractor specializing in finishes, he is right at home doing this sort of work, and as Peg will tell you, doing their own labor (aka, “sweat equity”) has saved them mad amounts of money.
However, when building a custom home, there’s a typical order of operations to follow when it comes to installing the mechanicals: first comes the HVAC unit and ducts (because they’re the largest), then plumbing/pipes, then the electrical lines (because they’re the most flexible), then drywall/plastering and so on. Tony knows the progression well, but even his house wasn’t going according to plan. Supply-chain issues and backordered materials meant that Tony had to take liberties with the sequence to stay on schedule.
“My husband is the OCD one, and he’s used to doing things in a certain order. I don’t know how it’s supposed to go so it doesn’t bother me,” says Peg with a chuckle.
In fact, throughout the roughly 12 months since Peg and Tony broke ground on their home, the supply chain has been their biggest hurdle. For example, they can’t set the kitchen island until downdraft comes in, and it’s backordered even though Peg reserved it five months ago. They also can’t get their septic system installed because there’s a national infiltrator shortage, which is problematic for anyone looking to build in the mountains.
“Just be up on it,” advises Peg to folks who find themselves in a similar boat. “I saw on the news that supply chains were cut, so I immediately ordered our cabinets last April. Tony thought I was nuts, but then it took nearly five months until they came in, and now no one can get them. Know where your supply chain is at, take it in stride and plan ahead as much as you can. You can’t get your knickers in a twist.”
Peg prefers to emphasize the good news over the challenges. For instance, the first floor is almost all drywalled. All the lights are up. She’s eagerly awaiting the installation of her granite, finished with a rugged leathered look that she describes as “the bomb.”
According to Bob Sternquist, owner and CEO of Timbercraft, the company that provided the couple’s timber frame package, Peg and Tony are part of a new breed of timber homeowners. Thanks to all the prep available through the internet, log and timber home shows and magazines like Log & Timber Home Living, they don’t rely on Bob to explain the fundamentals of timber framing or what diameter beam they need. Bob finds that homeowners like Peg and Tony are better informed than his clients were 25 years ago. They have a solid understanding of size and space, wood species and material options.
“I think one of the things that we do very, very well,” says Bob, “is explain to our customers what they can afford and how to get it. Through hybrid timber framing, which focuses the timbers in the high-use areas, we can make their dream come true. When people go to Peg and Tony’s house now, they believe she has this monster home on top of the world, but, really, it’s under 1,900 square feet. It’s grand, but it’s still intimate. It’s the quintessential timber home where you can stand in one corner and look all the way across the house.”
As for Peg and Tony, they’ve watched their home come together, piece by piece, from their temporary residence in an onsite RV. “We’re content,” says Peg. “I think I’d be way more wigged out if I wasn’t waking up here every day. I’m proud of ourselves for persevering through it all. More than anything, just expect things not to go to plan, be ready to make do and then figure out an alternative.”
Stay Tuned!
Join us as we navigate the design process with the homeowners and Timbercraft. You can find all the latest installments of the Dirt to Done series in the print magazine and here on timberhomeliving.com. Plus! Stay tuned for new webinars that dive into the process of creating this home.
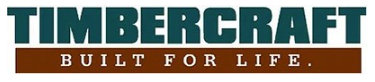