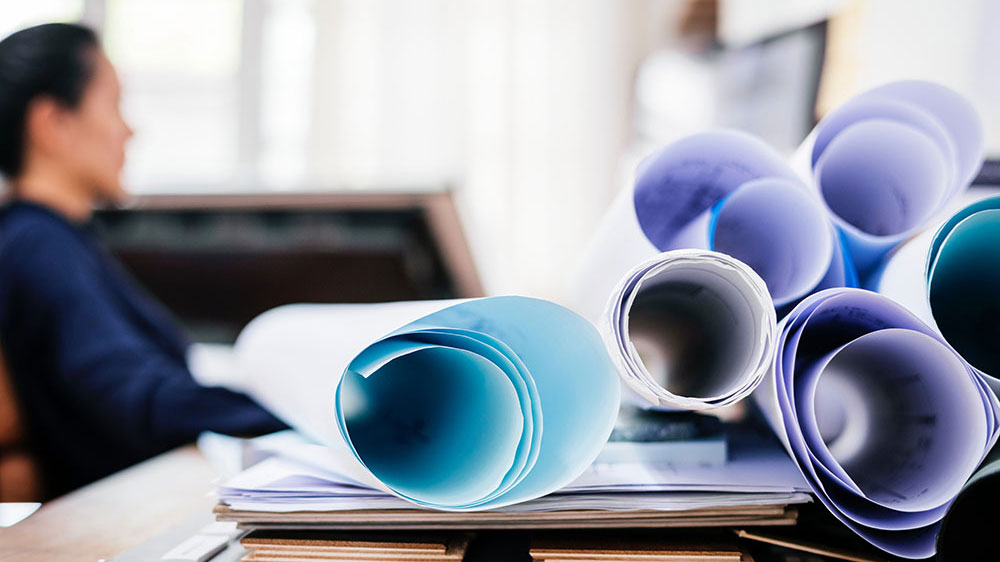
Dramatic design and overwhelming beauty draw many people to timber homes. Soaring cathedral ceilings and the warmth and sturdiness of exposed timbers provide a rustic elegance that is as comforting as it is awe-inspiring. Plus, who can argue with exceptional energy efficiency paired with Old World craftsmanship?
Those are only a few of the reasons people choose to live in a timber frame or post-and-beam home. Just as with log homes, deciding on the style of construction that’s right for you is often a matter of personal preference. Having an intimate knowledge of the construction techniques used in the frames isn’t necessary to love the look of these homes. However, a basic awareness of the terminology is necessary to choose a timber home provider and to understand what the inside and outside of your home will look like.
See Also: 4 Vital Questions to Ask as You Plan Your Timber Home
Defining Styles
In post-and-beam construction, vertical posts are connected to horizontal beams to create a structure’s load-bearing frame. They are most often wood, but they can also be steel or concrete. Post-and-beam structures are connected with metal fasteners that can include screws, nails and through-bolts. Timber framing, in contrast, is a specific style of post-and-beam construction that uses solid-wood timbers. Since this ancient building method originated before metal fasteners, the timbers use mortise-and-tenon joinery. This traditional form of joinery uses a wooden peg (tenon) from one timber that fits snugly into a hole or slot (mortise) of another.
Sometimes metal hardware is needed for additional strength or to satisfy building code requirements. In this instance, timber framers often will hide the connectors through a variety of trim applications. Some timber framers handcraft the timbers and joints with Old-World tools like chisels and mallets. Other producers use high-speed computer-controlled machines that make precise cuts that mimic the craftsmanship of old.
Be aware that your producer’s method of fabrication can affect the price for the package, length of time needed to construct it and delivery schedules.
See Also: What's the Difference Between Post-and-Beam and Timber Framing?
Enclosing the Frame
Producers may offer one or more options for enclosing the frame of your home. The difference between enclosure systems often is a matter of energy efficiency, function and form. Some provide a thick blanket to surround your timber frame, other enclosure systems offer the performance of a warm sweater. Your choice will likely by influenced by which producer you select and the climate of your region. When weighing your decision in choosing your timber frame producer and their enclosure system, keep in mind that four factors should influence your choice in enclosure systems: cost, ease of construction, energy performance and structural integrity.
By far the most popular method for enclosing timber frames is using structural insulated panels or “SIPs.” The reason for this is that SIPs can be quickly fastened to the frame, and they offer unsurpassed energy efficiency, reducing heating and cooling costs by as much as 60 percent over conventional 2-by-4 construction with batt insulation.
See Also: The Advantage of Using SIPs, or Structural Insulated Panels
Hybrids
Today’s timber home buyers are looking for a combination of conventional construction with a timber frame and log accents. Often called a “hybrid design,” buyers typically opt for timbers in the public areas (great room, foyer, kitchen dining area) and conventionally frame the more private spaces (bedrooms, bathrooms, mudrooms, garage, etc.). Log or timber frame accents are used on porches, decks and sometimes for exterior walls.
This is because timbers are more expensive, on average, and the cost competes with other upgrades, such as flooring, cabinetry and countertops. Often, it comes down to needs versus wants, tempered by practical trade-offs and guided by budget realities. Hybrid designs offer a good mix of budget control and beauty.
See also: Hybrid Floor Plans
What About Costs?
While it’s impossible to generalize costs nationwide, timber frame or post-and-beam homes are comparable in cost to other forms of custom construction. Put another way, custom construction averages 20 to 30 percent more than those from your local production or tract builder, who offers few upgrades and no alterations to designs.
With all things being equal in regards to square footage and amenities, hybrid designs can save buyers roughly $10 to $15 per square foot, or 5 to 10 percent, over a home that uses a full timber framed structure.
See Also: 5 Money-Saving Tips for Your Timber Home
What is different about finishing timber frames?
Construction with a timber frame differs from the current convention, 2-by-4 or 2-by-6 construction, but these differences don’t need to lead to increased difficulty or inflated costs. Being aware of these differences early on can help you understand building process and important design questions.
Foundation.
Foundations for timber frames must account for point loading (where the posts are supported), which is different from conventional building requirements. To assure that the precut frame will fit well, foundation-construction precision is critical. It is also important to ensure that the foundation resists uplift loads from wind and earthquakes. Timber frame builders and engineers will provide fastener requirements to your foundation subcontractor.
Doors and windows.
Depending on the enclosure system used, deeper jambs may be required for doors and windows.
Drywall and painting.
You may need extra taping and prep time as you work around visible timber beams and decorative wood.
Electrical.
Electrical wiring of interior walls is not radically changed. However, if a timber-framed structure is enclosed with structural insulated panels (SIPs), the SIPs will require a precut chase to allow for wiring of exterior walls.
Plumbing, HVAC and ductwork.
These should be run in interior walls and laid out to avoid interfering with structural members. If using SIPs, plan to do an energy audit and ventilate the building.
See Also: 11 Tips to the Perfect Timber Home
Timber Home Producer Checklist
-
When shopping for a timber home producer, use these questions to help you make your decision:
-
What kind of product does the company offer? Post-and-beam? Timber frame? Both?
-
How do they fabricate their frames? Are they handcrafted or milled by machines?
-
What is the average length of time between final design and delivery of home package?
-
What kind of enclosure systems do they recommend?
-
What is the advantage of their building system?
-
How will this affect cost, ease of construction, energy performance, structural integrity?