Want to show your patriotic pride by buying American? Know the facts first.
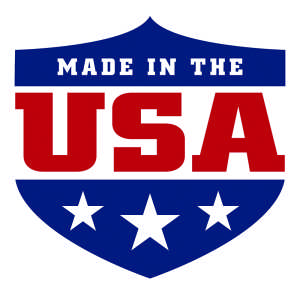
He found that the products — from flooring to nails, to hinges, to windows — did not necessarily cost more, but he faced additional labor costs because of the amount of time it took to source everything. “I had to call distributors and manufacturers to find out if all of a product’s components were American made,” he says.
Most consumers are likely not as exacting as Pike’s client, but plenty of them want American-made products. In fact, a 2013 Consumer Reports survey found that 78 percent of Americans would rather buy an American product than one made abroad. Pike now sees using American-made products for his projects as “a great selling point” and offers it as an option to all his clients. But how do you know you’re building products are truly made in America?
Manufacturers such as Marvin have used the “Made in America” tag for a number of years, and “most of our raw materials and all of our assembly is in the United States,” says regional sales manager Doug Johannson. Senco, which produces over 700 varieties of staples and nails in its Cincinnati facility, puts American flags on its product boxes. The Triple A Building Center, a member of the Do-It Best Co-Op, has labels and flags that it puts on its shelves.
There are a lot of products labeled “Made in the USA” or “Made in America.” Some are assembled in America using products from abroad. Some are wholly made in the United States. The U.S. Federal Trade Commission has rules against deceptive claims, and, according to its website, “‘Made in USA’ means that ‘all or virtually all’ the product has been made in America. That is, all significant parts, processing, and labor that go into the product must be of U.S. origin.”
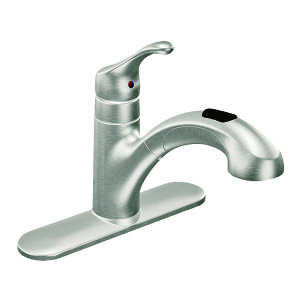
Four years ago, Bozeman, Montana, builder Anders Lewendal challenged himself to build a home for a client using only American-made products. He says it added only “one to two percent more in costs and no additional time. There is not a product in the house that was not produced in America.”
Lewendal created a website called TheAllAmericanHome.com, which tells the story of the project and includes a list of the 181 building products he used — everything from “J bolts/foundation/stock” from Utah’s Pacific Steel to “8d ring shank nails” from True Spec in California to foam board by Dow in Illinois; Sherwin Williams paint in Ohio; ductwork from Norwesco in Washington State; plywood from Potlach in Idaho; and plumbing fixtures from Moen in North Carolina.
Lewendal also helped with 84 Lumber’s “We Build American” campaign introduced at the 2013 International Builders Show. More than 180 building material companies in more than 40 states joined the initiative. “A lot of people think we don’t make stuff in America, but the truth is we produce more things than anywhere else in the world,” Lewendal says. While Lewendal is now determined to use American-made products on each building project, he admits that sometimes a better product is produced overseas.
“We’re not here to waste money,” he says, but he feels strongly enough about purchasing American products that he has “forced suppliers to make an equal or better product.”